Основной целью магистерской работы является оптимизации процесса горячего прессования металлических порошков, разработка новых технических решений для установки горячего прессования, с целью увеличения ее производительности и минимизация энергозатрат.
Актуальность темы магистерской работы. На сегодня, с созданием и внедрением прогрессивных ресурсосберегающих технологий и новой техники важным аспектом научно-технического прогресса является появление новых способов получения материалов и изделий с заданными или принципиально новыми свойствами. К таким материалам относятся продукты порошковой металлургии. Благодаря структурным особенностям изделия их них более термостойки, лучше переносят воздействие циклических колебаний температуры и напряжения, а также ядерного облучения, что очень важно для материалов новой техники. А новые материалы, создаваемые методами порошковой металлургии, являются в ряде случаев основой коренного улучшения существующих и создания новых технологических процессов в машиностроении, металлургии, химической и других отраслях промышленности.
Порошковая металлургия имеет и недостатки, тормозящие ее развитие, к ним относится сравнительно высокая стоимость металлических порошков, производственные расходы связанные с изготовления индивидуальных приспособлений (пресс-форм), необходимость спекания в защитной атмосфере, что увеличивает себестоимость изделий порошковой металлургии, сложность получения металлов и сплавов в компактном состоянии, необходимость применения чистых исходных порошков для получения чистых металлов. Но недостатки порошковой металлургии и некоторые ее достоинства нельзя рассматривать как постоянно действующие факторы, в значительной степени они зависят от состояния и развития не только самой порошковой металлургии, но и других отраслей промышленности. С увеличением масштабов выпуска и совершенствованием методов порошковой металлургии большинство из этих проблем решится. По мере развития техники, порошковая металлургия приобретет большее значение в развитии научно-технического прогресса в промышленно развитых странах, проникнет во все отрасли народного хозяйства и поможет решить многие сложнейшие проблемы развития новой техники.
1.ОБЩИЕ СВЕДЕНИЯ О ПОРОШКОВОЙ МЕТАЛЛУРГИИ
Сущность порошковой металлургии заключается в том, что из металлического порошка или смеси порошков прессуют заготовки, которые затем подвергают термической обработке – спеканию.
Порошковая металлургия и дальнейшая перспектива ее развития
... прессования и формования изделий из порошков. Первые систематические исследования выполненные в 1936 - 1937 гг. положили начало развитию работ в этой области. Исследованы закономерности прессования в пресс-формах, ... Типовая технология производства заготовки изделий методом порошковой металлургии включает четыре основные операции: получение порошка исходного материала; формование заготовок; спекание и ...
Порошковой металлургией можно получать детали из особо тугоплавких металлов, из нерастворимых друг в друге металлов (вольфрам и медь, железо и свинец и т. д.), пористые материалы и детали из них, детали, состоящие из двух (биметаллы) или нескольких слоев различных металлов и сплавов. Металлические порошки состоят из очень мелких частиц (0,5–500 мкм) различных металлов и их окислов. Порошки получают механическим и физико-химическим путем.
Для механического измельчения твердых и хрупких материалов применяют шаровые, вибрационные мельницы и бегуны. Порошки из пластичных и легкоплавких металлов и сплавов получают различными способами, основанными на раздуве жидкого материала струей воды или газа. Механическим путем, как правило, получают порошки из отходов основного производства
К физико-химическим способам получения порошков относят восстановление окислов металлов, электролиз и др
Окислы металлов можно восстанавливать газообразными или твердыми восстановителями. Наибольшее практическое применение нашли газообразные углеродистые и углеводородистые соединения (природный газ, доменный, углекислый газ) и водород. Электролизом водных растворов солей получают тонкие и чистые порошки различных металлов и сплавов. Порошки из редких металлов (тантала, циркония, титана и др.) получают электролизом расплавленных солей. Режимы и технология изготовления порошков физико-химическим путем приведены в справочной литературе [1,2].
Основными технологическими свойствами порошков являются текучесть, прессуемость и спекаемость.
Текучесть — способность порошка заполнять форму. Текучесть ухудшается с уменьшением размеров частиц порошка и повышением влажности. Количественной оценкой текучести является скорость вытекания порошка через отверстие диаметром 1,5–4,0 мм в секунду.
Прессуемость характеризуется способностью порошка уплотняться под действием внешней нагрузки и прочностью сцепления частиц после прессования. Прессуемость порошка зависит от пластичности материала частиц, их размеров и формы и повышается с введением в его состав поверхностно-активных веществ.
Под спекаемостъю понимают прочность сцепления частиц в результате термической обработки прессованных заготовок.
Одной из главных операций при производстве порошковых изделий, является формование тел из металлических порошков. При формовании в основном определяются форма и размеры изделий. Для формования компактного тела из порошка требуются значительные затраты энергии. Эта энергия расходуется на уплотнение заготовки путем перемещения и деформации частиц, на преодоление сил трения между частицами и стенками формующей полости.
Чем больше контактная поверхность частиц порошка, тем сильнее между ними зацепление и сцепление. А площадь контакта, естественно, увеличивается при повышении давления на поверхность. За счет увеличения контакта между частицами при формовании повышается прочность формуемого тела, уменьшается пористость, измельчаются скопления частиц, а иногда и сами частицы, и происходит некоторое упрочение частиц.
Порошковые металлы могут деформироваться как вследствие деформации отдельных частиц, так и вследствие их смещения и заполнения ими пор. Таким образом, деформация сыпучего тела, в отличие от компактного, изменяет не только его форму, но и объем. Обычно при формовании высота заготовки по отношению к высоте насыпанного порошка уменьшается в 3–4 раза и более.
Технология изготовления изделия из металлических порошков
... невозможно, опять обратились к технологии изготовления изделий методами порошковой металлургии. Это ... металлов и изделий из них. Известно, что уже в глубокой древности (до нашей эры) порошки ... частиц на более мелкие частицы. Процесс протекает более интенсивно, чем в шаровых мельницах. Получающиеся частицы порошка ... соединений — отличаются тем, что получаемый порошок по химическому составу существенно ...
При формовании может происходить одновременно упругая, хрупкая и пластическая деформация частиц. Рисунок 1 показывает возможные схемы перемещения частиц порошкового металла. При сближении частиц может происходить увеличение площади контактных участков как без деформации частиц (а), так и с их деформацией (б); удаление частиц (в) вызывает уменьшение контактных участков и даже может привести к разрыву контакта; скольжение частиц (г) сопровождается смещением контактных участков; одновременно с перемещением частицы могут разрушаться вследствие хрупкой деформации (д).
В результате хрупкой деформации могут разрушаться как скопления частиц, так и сами частицы. Это наблюдается при формовании порошков с хрупкими и твердыми составляющими, например тонкой чугунной стружки, а также твердых, но хрупких соединений металлов. Степень деформации частиц повышается с увеличением пластичности формуемого материала и прилагаемого давления.
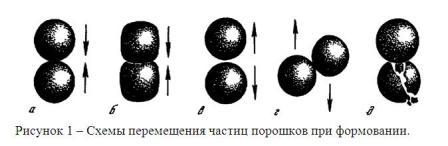
На результаты формования оказывают влияние различные факторы: насыпная масса порошка, предварительная обработка порошков, величина и направление давления при формовании и др.
Сыпучие тела занимают объем, при котором механическая прочность тела, обусловленная взаимным зацеплением частиц, достаточна для сопротивления давлению, вызываемому массой порошка. Если механическая прочность велика, то достаточная степень зацепления получается уже при рыхлой укладке и порошок имеет малую насыпную массу. Если же прочность сыпучего тела мала, то для получения необходимого зацепления нужна более плотная укладка, что повышает насыпную массу порошка [2,3].
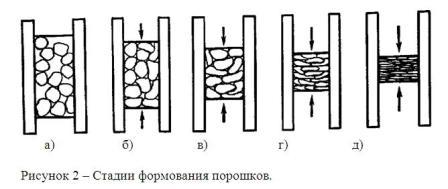
При засыпке порошка в пресс-форму его частицы располагаются хаотически, образуя при этом так называемые мостики или арки. Плотность засыпанного порошка в этом случае равна его насыпной массе (рис.2, а).
Приложение внешнего давления к такому свободно насыпанному порошку приводит к резкому повышению его плотности за счет заполнения пустот и пор. По мере увеличения прилагаемого давления мостики и арки разрушаются (рис. 2, б, в) и частицы проникают в мелкие поры. На дальнейших этапах формования происходит качественное и количественное изменение границ между частицами. От трения частиц при перемещении друг относительно друга сдираются окисные пленки, контакты между частицами в этих местах из неметаллических переходят в металлические, в результате чего повышается прочность заготовки (рис. 2, г); затем происходит хрупкое разрушение частиц порошков из твердых металлов и пластическая деформация частиц из мягких металлов (рис. 2, д).
Прессование и волочение
... уменьшается величина давления, необходимого для уплотнения порошка. Метод горячего прессования позволяет получать изделия из порошков, не поддающихся формованию или спеканию обычными способами. При горячем прессовании увеличение контакта между частицами достигается: ...
Методы формования порошковых заготовок весьма разнообразны. По времени действия их можно подразделить на прерывистые и непрерывные, по принципам приложения давления – на постепенно возрастающие, мгновенно возрастающие и вибрационные, по направлению или схеме формования – на односторонние, двусторонние, всесторонние и центробежные, по применяемой температуре – на холодное формование при комнатной температуре и горячее при повышенной, по атмосфере – на формование на воздухе, в вакууме и в инертной среде.
2.ГОРЯЧЕЕ ПРЕССОВАНИЕ МЕТАЛЛИЧЕСКИХ ПОРОШКОВ
2.1 Виды спекание порошковых материалов
Термическая обработка, позволяющая получить конечные свойства материала и изделия, называется спеканием. Оно заключается в нагреве и выдержке сформованного изделия (заготовки) при температуре ниже точки плавления основного компонента. Для многокомпонентных систем различают твёрдофазное и жидкофазное спекание.
Твёрдофазное спекание сопровождается возникновением и развитием связей между частицами, образованием и ростом контактов (шеек), закрытием сквозной пористости, укрупнением и сфероидизацией пор, уплотнением заготовки за счёт усадки. В процессе спекания происходит массоперенос вещества через газовую фазу за счёт поверхностной и объёмной диффузии, вязкого течения, течения, вызванного внешними нагрузками (спекание под давлением).
При спекании наблюдается также рекристаллизация (рост одних зёрен за счёт других той же фазы).
Уплотнение при нагреве в основном происходит за счёт объёмной деформации частиц, осуществляемой путём объёмной самодиффузии атомов [4].
Жидкофазное спекание протекает в присутствии жидкой фазы легкоплавкого компонента, которая хорошо смачивает твёрдую фазу, улучшает сцепление между частицами, увеличивает скорость диффузии компонентов, облегчает перемещение частиц друг относительно друга. Плохая смачиваемость препятствует уплотнению. Твёрдая фаза в зоне контакта может растворяться в жидкой, интенсифицируя процессы массопереноса. Различают системы с нерастворимыми компонентами, с ограниченной растворимостью и со значительной взаимной растворимостью компонентов. Жидкофазное спекание таких систем имеет свои особенности, связанные с преобладанием одной из стадий:
- вязкое течение жидкости – перегруппировка частиц;
- растворение – осаждение; образование жёсткого скелета.
Совмещение процесса прессования и спекания наблюдается при горячем прессовании, которое производится при температуре (0,5…0,9) Тпл основного компонента. Это позволяет использовать увеличение текучести шихты при повышенных температурах с целью получения малопористых изделий. В этом случае силы давления формования суммируются с внутренними физическими силами приводящими к уплотнению [7].
Стадийность процессов, происходящих при горячем прессовании, во времени можно проиллюстрировать рисунком 3, где имеется три основных стадии:
1. До 90 % от максимально достижимой плотности реализуется сдвиг и скольжение частиц относительно друг друга;
2. Граничное скольжение частиц и объёмная деформация;
3. Объёмная деформация.
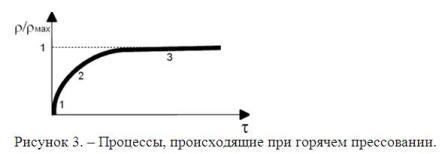
Технология производства макаронных изделий
... макаронных предприятий используют то или иное оборудование. Оборудование складов муки предназначено для приемки, хранения и транспортирования ее внутри склада и к макаронным прессам, а также подготовки к производству ...
Наиболее существенными результатами горячего прессования являются максимально быстрое уплотнение и получение изделия с минимальной пористостью при сравнительно малых давлениях. Механизм уплотнения идентичен наблюдаемому при обычном спекании: образование межчастичного контакта, рост плотности с одновременным увеличением размеров частиц и дальнейший рост частиц при незначительном дополнительном уплотнении. Изделия после горячего прессования обладают более высоким пределом текучести, большим удлинением, повышенной твердостью, лучшей электропроводностью и более точными размерами, чем изделия полученные путем последовательного прессования порядка и спекания. Указанные свойства тем выше, чем больше давление прессования. Горячепрессованные изделия имеют мелкозернистую структуру [6,8].
Процессы спекания при обычном методе раздельного прессования и спекания длятся 1 – 2ч, в то время как при горячем прессовании длятся всего 3 – 15 мин.
Материалом для изготовления пресс-форм служат жаропрочные стали (при температурах до 1000оC) графит, силицированный графит, имеющий повышенную механическую прочность. В настоящее время расширяется применение пресс-форм из тугоплавких окислов, силикатов и других химических соединений. С целью предотвращения прилипания спекаемых изделий к рабочим частям графитовой пресс-формы, что влечет за собой необходимость разрушения пресс-формы после каждого спекания, внутренние стенки матрицы и поверхность пуансонов, прилегающих к прессуемому материалу, перед горячим прессованием покрывают специальными смазками, например суспензией жирного чешуйчатого графита в глицерине, инертным составом (жидкое стекло, эмаль, нитрид бора др.) или металлической фольгой. Кроме того, для предупреждения окисления прессуемого изделия применяют защитные среды (восстановительные или инертные) или вакуумирование.
Нагрев пресс-форм и материала осуществляется одним из следующих способов (рис. 4).
>применением внешних нагревателей (а);
- >непосредственным пропусканием тока через пресс-форму (б);
- >непосредственным пропусканием тока через порошок (в);
- >индукционным высокочастотным нагревом (г).
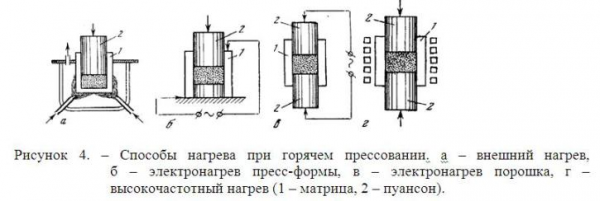
2.2 Оборудование для горячего прессования
Горячее прессование выполняют на специальных гидравлических прессах, имеющих устройства для регулирования температуры при прессовании (рис. 5).
Основными узлами установки являются: пресс гидравлический (1), обеспечивающий усилие прессования 120 тс, вакуумная камера (2), выполненная из нержавеющей стали, со встроенными в нее медными башмаками, источник питания (3), предназначенный для нагрева пресс-формы.
Камера (2) соединена с источником питания (3) гибкими медными водоохлаждаемыми токоподводами (4).
Регулировка мощности источника питания, а также управление всеми системами установки осуществляется с помощью электрошкафа (5).
Работа пресса обеспечивается гидроагрегатом (6), который оснащен тремя насосами: холостого хода, рабочего хода и управляющего давления.
Вакуумирование камеры обеспечивается вакуумной системой (7), рабочий вакуум составляет ~ 1 Па (в холодном состоянии).
Порошковая металлургия
... стоимость металлических порошков значительно превышает стоимость литых металлов. Развитие порошковой металлургии обусловлено главным образом тем, что её технологические операции сравнительно ... операция получения изделия или заготовки заданной формы, размеров и плотности обжатием сыпучих материалов (порошков). Уплотнение порошка осуществляется прессованием в металлических пресс-формах или эластичных ...
Напуск рабочего газа в камеру и контроль рабочей среды внутри камеры обеспечивает система газообеспечения (8).
Система водоохлаждения (9) предназначена для охлаждения выпрямителя источника питания, стенок вакуумной камеры, гибких токоподводов и медных башмаков.
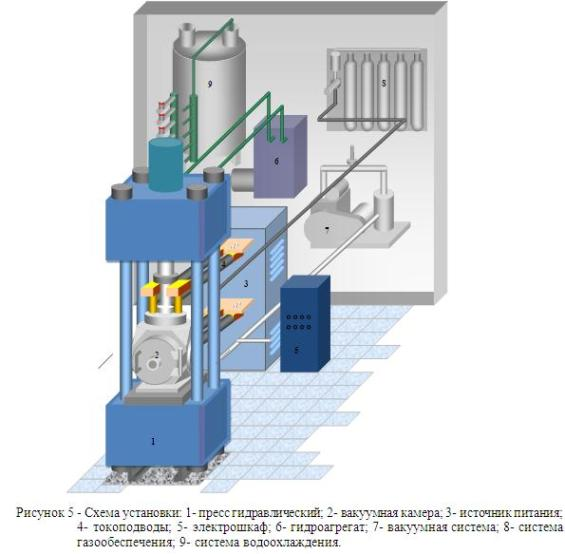
Сама технология представляет собой следующие действия. Предварительно сформованные изделия из порошкового материала помещают слоями внутри пресс-формы и заполняют специальным графитовым порошком, который выполняет функцию упруго-сжимаемой среды (рис. 6), затем пресс-форму в сборке помещают в вакуум-камеру. В процессе прессования давление от пуансонов передается на изделия через графитовый порошок [9,10].
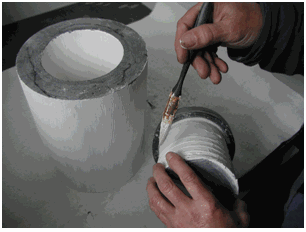
Анимация — Подготовка пресс-формы (4 кадра, интервал — 1,3 с., размер 103 Кб.)
Механизм уплотнения включает образование механического контакта, рост плотности с одновременным увеличением размеров частиц и дальнейший рост частиц при незначительном дополнительном уплотнении.
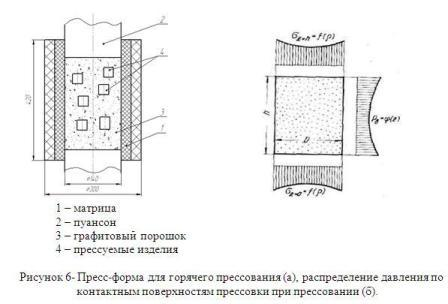
3. ПРАКТИЧЕСКАЯ ЧАСТЬ МАГИСТЕРСКОЙ РАБОТЫ
Важным требованием при изготовлении изделий методом горячего прессования является обеспечение геометрической формы с заданными размерами. Полученные ранее результаты свидетельствуют, что горячее прессование в упругосжимаемой среде приводит к неравномерной деформации изделий. В направлении приложения усилия прессования деформация значительно превышает деформацию в плоскости, перпендикулярной оси прессования. Это связано с тем, что в процессе прессования, внешнее трение прессуемых порошковых тел о контактные поверхности элементов пресс-форм приводит к значительному перераспределению давлений и плотности. За один цикл прессования на рассматриваемой установке формируется не более 5-6 изделий. Сложность передачи давления не позволяет качественно пропрессовать большее количество образцов. Действие сил трения приводит к необходимости повышать давление прессования, а также является причиной неравномерности плотности в изделиях. Исследованию этого вопроса посвящены работы многих специалистов в этой области.
Однако анализ напряженного состояния материала и изделий при их взаимодействии показывает, что можно увеличить производительность установки за счет применения промежуточных прокладок, закладываемых внутрь пресс-формы между слоями материала и образцов. Это позволит за счет перераспределения напряжений в пресс-форме обеспечить более равномерное наложение давления на изделие и изготавливать большее количество изделий за один цикл прессования, улучшив их характеристики. Еще больший эффект возможно получить при установке изделий под углом 45 градусов, применением закладных элементов повышенной прочности и пр.
Минеральная и стеклянная вата и изделия на их основе
... основе металлургических шлаков и других побочных продуктов промышленности. Также минеральная вата - это волокнистый бесформенный материал - состоит из тонких расплавов стекловидных волокон диаметром 5-15 мкм, получаемых из расплава ... мешки, а также хлопчатобумажную ткань или рогожу. Хранят стеклянную вату и изделия из нее в крытых сухих помещениях, транспортируют в крытых вагонах или автомашинах. ...
Повышение производительности установки приведет к уменьшению энергозатрат для изготовления изделий, сделает их более доступными для широкого круга потребителей.
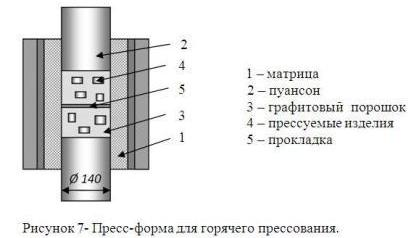
Дальнейшие исследования для магистерской работы будут направлены на изучение этого вопроса. На данном этапе идет разработка математической модели процесса горячего прессования при использовании закладных элементов различного профиля.
Список литературы
[Электронный ресурс]//URL: https://drprom.ru/referat/goryachee-pressovanie/
- Жданович Г.М. Теория прессования металлических порошков /Г.М. Жданович // «Металлургия», М., 1969. – 256 с.
- Либенсон Г.А. Порошковая металлургия /С.С. Кипарисов, Г.А. Либенсон// «Металлургия», М., 1980. – 496 с.
- Бальшин М.Ю. Основы порошковой металлургии /М.Ю. Бальшин, С.С. Кипарисов// «Металлургия», М., 1978. – 185 с.
- Генералов М.Б. Механика твердых дисперсных сред в процессах химической технологии: Учебное пособие для вузов /М.Б. Генералов // Калуга: Издательство Н. Бочкаревой, 2002. – 592 с.
- Бальшин М.Ю. Научные основы порошковой металлургии и металлургии волокна/ Бальшин М.Ю.,// М., «Металлургия», 1972. – 347 c.
- Федорченко И.М. Основы порошковой металлургии/ И.М. Федорченко ,Р.А. Андреевский // Киев, 1963. – 420 с.
- Остапенко И.Т. Уплотнение порошка карбида бора при горячем прессовании / И.Т. Остапенко, В.В. Слезов, Р.В. Тарасов // Порошковая металлургия, 1979. – 129 c.
- Ковальченко М.С. Теоретические основы горячей обработки пористых материалов давлением /М.С. Ковальченко // Киев: «Наукова думка», 1980. – 238 с.
- Angers R. Hot pressing or boron carbide/R. Angers, M. Beauvy // Ceram. Intern, 1984. – pp. 49-55.
- Розанов Б.В. Гидравлические прессы / Б.В. Розанов // М.: Машиностроение, 1959. – 425 с.