В данной работе рассмотрены вопросы, связанные с автоматизацией системы пожаротушения сушильного цеха АО «Апатит». При автоматизации особе внимание необходимо уделять выявлению пожара, поддержанию требуемого давления в трубопроводах системы пожаротушения и наполнению пожарного резервуара. Реализация данной системы автоматизации может быть выполнено в рамках действующего производства.
Глава 1. Описание технологического процесса сушильного цеха
ФСПО АНОФ-2 объединяет технологические процессы обезвоживания (фильтрация и сушка) пульпы, поступающей из главного корпуса, погрузки высушенного концентрата в силосные банки и технологический процесс очистки отходящих газов. Таким образом, корпус подразделяется на три отделения: фильтрации, сушки и газоочистки.
Процесс сушки осуществляется на 11-и идентичных технологических нитках. На рис. 1.1 представлена технологическая схема одной нитки ФСПО АНОФ-2.
Пульпа из центрального пульподелителя (ЦПД) подается в секционный пульподелитель и оттуда распределяется по вакуум-фильтрам (5-6 на нитку).
Полученный в вакуум-фильтрах кек с влажностью 10-12% с помощью ленточного конвейера (КЛ) сбрасывается в загрузочную камеру сушильного агрегата, который состоит из топки и сушильного барабана. Сушильным агентом являются газы, образованные в топке при сжигании высокосернистого мазута в среде, создаваемой первичным воздухом. Транспортировка сушильных газов осуществляется дымососом, создающим необходимое для их движения разрежение по тракту их следования. Для охлаждения свода печи в топку подается вторичный воздух.
Сушка кека производится в сушильных барабанах диаметром 3.5 м и длиной 27 м. Сушильный барабан имеет уклон по оси в сторону разгрузочной камеры, благодаря чему при его вращении со скоростью 4.5 об/мин. материал внутри барабана, пересыпаясь с полки на полку, перемещается по длине барабана в сторону разгрузочной камеры. Высушенный материал с Wк=1-1.5% через разгрузочную камеру подается по сборному конвейеру (КС) на силосный склад, где реверсивным конвейером (КР) распределяется по силосным банкам (три на каждый агрегат), откуда загружается в железнодорожные вагоны.
Отходящие газы на выходе из сушильного барабана очищаются от пыли в батарейных циклонах, электрофильтрах и водяных скрубберах, после чего выбрасываются в атмосферу. Вода, подаваемая в скруббера, смешивается с каустиком для нейтрализации стоков.
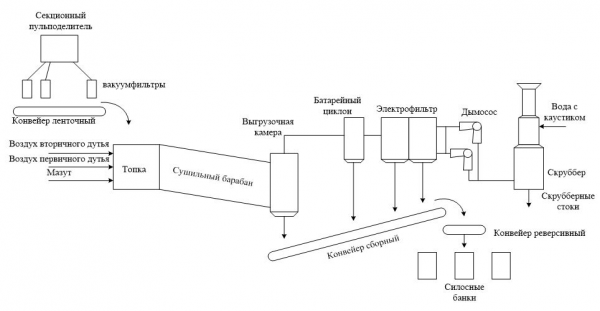
1.1. Характеристика производимой продукции
Разработка системы электроснабжения буровой установки
... проекте рассмотрено энергоснабжение буровой установки HR-5000. В установке реализованы система верхнего привода, и комплексная автоматизированная система управления. В проекте рассмотрены преимущества этих системы, оценена экономическая ... 12"марта 2012 г. Г. В. Самбуров (подпись студента) (расшифровка подписи) РЕФЕРАТ Дипломная работа включает в себя пояснительную записку, состоящую из 104 страниц ...
Апатитовый концентрат является основным продуктом обогащения апатито-нефелиновой руды и представляет собой кристаллический порошок серого цвета, содержащий 95-97% чистого минерала апатита, имеющий удельный вес 3,15-3,20 т/м3. Апатитовый концентрат выпускается согласно техническим требованиям ГОСТ 22275-90.
Примерный минералогический состав апатитового концентрата, %:
апатит 94,5-95,8
нефелин 2,1-3,0
полевой шпат 0,1-0,2
эгирин 0,2-0,5
сфен 0,4-0,7
титаномагнетит следы
Апатитовый концентрат применяется как высококачественное сырье для производства фосфорсодержащих минеральных удобрений, элементарного фосфора, фосфорной кислоты и других фосфорных соединений. Апатитовый концентрат отличается от других фосфатов постоянством состава, повышенным содержанием пятиокиси фосфора, малым содержанием окиси магния, органики, хлора, кадмия, мышьяка, тяжелых металлов, что, в конечном итоге, предопределяет его технологичность при переработке и экологическую чистоту. Он содержит также фтор, окиси стронция и редкие земли, которые могут выделяться при переработке в отдельные продукты. Его химический состав в 1998 г. сертифицирован немецкой компанией «TUV Suddeutschland Standard UPZ».
1.2. Технологический регламент
Таблица 1.1. Контроль производства и управление технологическим процессом
Наименование стадий процесса, места измерения параметров | Контролируемый параметр | Частота и способ контроля | Норма и технический показатель | Метод испытания и средство контроля. | Погрешность результатов измерений не превосходит | Кто контролирует. |
Сушка апатитового концентрата | Влажность концентрата после сушильных барабанов | Непрерывно, автоматически | Зима 0,5¸1,5 % влаж.
Лето 1,0-2,0 % влаж. |
Влагомер-АСУ | 0,2 % влаж. | Оператор, АРМ оператора |
Давление мазута на входе в топку | Непрерывно, автоматически | 0,2 МПа
(0,05-0,2) |
Измерительный преобразователь давления-АСУ | 10 кПа | ||
Мощность двигателя | Непрерывно, автоматически | 0-100 % | Измерительный преобразователь тока, нормирующий преобразователь-АСУ | 1 % | Оператор, АРМ оператора | |
Массовый расход мазута | Непрерывно, автоматически | 1260 кг/час
(1050-1500) |
Расходомер-АСУ | 20 кг/час | ||
Разряжение в разгрузочной камере | Непрерывно, автоматически | 0,20-0,25 кПа | Измерительный преобразователь давления-АСУ | 0,005 кПа | ||
Разряжение в топке | 0,03-0,1 кПа | Измерительный преобразователь давления-АСУ | 0,002 кПа | |||
Расход воздуха вентиляторов ВДВ | Непрерывно, автоматически | 3000-8000 м 3 /час | Измерительный преобразователь давления-АСУ | 150 м 3 /час | ||
Расход воздуха вентиляторов ВД | 11000-30000 м 3 /час | Измерительный преобразователь давления-АСУ | 300 м 3 /час | |||
Температура в топке | Непрерывно, автоматически | 900-1200 °С | Датчик температуры, нормирующий преобразователь-АСУ | 1,5 °С | ||
Температура газов после сушильных барабанов | 110 °С
(90-130) |
Датчик температуры-АСУ | ||||
Сушка апатитового концентрата | Температура концентрата после сушильных барабанов | Непрерывно, автоматически | не более 80 °С | Датчик температуры, нормирующий преобразователь температуры-АСУ | 1,5 °С | Оператор, АРМ оператора |
Температура мазута | 95-115 °С | |||||
Температура газов перед сушильными барабанами | 900-950 °С |
Таблица 1.2. Аналитический контроль производства
Сухой апатитовый концентрат после сушильных барабанов. | Массовая доля Р 2 О5 | Ручной отбор проб 1 раз в час, общий анализ по всем работающим с/барабанам. Анализ по каждому барабану 1 раз в 4 часа. | Стандартный не менее 39,00 %, | Химический анализ трилонометрическим методом. | 0,2 % | Начальник смены, диспетчер фабрики. |
Ручной отбор проб 1 раз в час. Анализ 1 раз в 2 часа. | «Супер» – не менее 40,0 % | |||||
Массовая доля класса +0,16 мм | Анализ общий по всем барабанам 1 раз в час и среднесменный. | Стандартный — не более 13,5 % | Метод сухого рассева. | 1,5 % | Начальник смены, диспетчер фабрики. | |
Анализ 1 раз в час и среднесменный. | «Супер» – не менее 32,0 % | |||||
Массовая доля влаги | Анализ 1 раз в час по каждому барабану и общий анализ по всем с/барабанам. Среднесменный (расчет) | Май-сентябрь- 1,0-2,0 %Остальные месяцы- 0,5-1,5 % | Влагомеры. | 0,15 % | Начальник смены, оператор с/б, диспетчер фабрики | |
Готовый апатитовый концентрат (погрузка) |
Массовая доля Р 2 О5 |
Автоматический отбор проб 1 раз в 5 минут.
Анализ 1 раз в час. |
Стандартный — не менее 39,0 %;
«Супер» – не менее 40,0% |
Химический анализ титриметрическим висмутатным методом | 0,3 % | Начальник смены, мастер ОП, диспетчер фабрики. |
Массовая доля класса +0,16 мм | Стандартный — не более 13,5 % ;
«Супер» – не менее 32,0 % |
Метод сухого рассева. | 1,50 % | |||
Массовая доля влаги | Май-сентябрь- 1,0-2,0 %
Остальные месяцы-0,5-1,5 % |
Анализатор влажности МА 30 фирмы «SARTORIUS». | 0,15 % |
1.3. Пожароопасное оборудование и пожароопасные участки
Приведенное выше описание цеха, технологического процесса и выпускаемой продукции свидетельствуют о высокой пожароопасности сушильного цеха.
Особенно выделим следующие участки цеха, в которых установлены элементы системы автоматического пожаротушения:
- участок секционного пульпоотделителя;
- участок ленточного конвейера;
- участок сушильного барабана;
- участок конвейера сборного;
- участок скруббера;
- другие участки сушильного цеха.
Глава 2. Назначение системы автоматизации пожаротушения
Комплексная система автоматического пожаротушения сушильного цеха АНОФ-2 ФОСАГРО «Апатиты» предназначена для автоматизации пожаротушения помещений и технологического оборудования сушильного цеха.
Система пожаротушения предназначена для предотвращения, ограничения развития, тушения пожара, особенно на ранних стадиях, а также защиты от пожара людей и материальных ценностей [ 5].
система автоматического пожаротушения (АУПТ)
Наиболее эффективными являются комплексные решения, объединяющие систему пожаротушения с системами пожарной сигнализации (СПС) и системами оповещения и управления эвакуацией (СОУЭ).
Порядок и необходимость установки автоматического пожаротушения регламентируется нормативными документами, такими как: НПБ 110-03 (Нормы пожарной безопасности «Перечень зданий, сооружений, помещений и оборудования, подлежащих защите автоматическими установками пожаротушения и автоматической пожарной сигнализацией»).
В обязательном порядке системами автоматического пожаротушения оборудуются серверные комнаты, архивы, помещения с размещением электроустановок и другие помещения для хранения и обработки информации, автостоянки закрытого типа (подземные и надземные при 2-х этажах и выше), а также складские помещения, торговые залы, ремонтные мастерские и другие производственные и непроизводственные помещения, в зависимости от занимаемой ими площади и характера хранимых материалов.
Защищаемые объекты системой автоматического пожаротушения:
- участок секционного пульпоотделителя;
- участок ленточного конвейера;
- участок сушильного барабана;
- участок конвейера сборного;
- участок скруббера;
- другие участки сушильного цеха.
В качестве исполнительных устройств системы автоматического пожаротушения выступают:
- резервуары противопожарного запаса воды;
- насосы подачи воды, объектовые задвижки пожаротушения;
- пожарные извещатели, устройства светового и звукового оповещения.
Система выполняет следующий объем функций:
- прием электрических сигналов от ручных и автоматических пожарных извещателей с индикацией номера сработавшего датчика или шлейфа пожарной сигнализации;
- контроль исправности шлейфов ручных извещателей по всей их длине с автоматическим выявлением обрыва или короткого замыкания;
- контроль замыкания шлейфов и линий связи на землю;
- автоматический пуск огнетушащего вещества на защищаемый объект (запуск необходимых насосов и открытие запорной арматуры);
- задержка выпуска огнетушащего вещества в защищаемое помещение, где возможно нахождение людей;
- отключение автоматического пуска оборудования пожаротушения с сохранением возможности местного (ручного) пуска;
- автоматический контроль исправности электрических цепей исполнительных механизмов, цепей системы оповещения и датчиков технологических параметров;
- автоматический контроль уровней в резервуарах противопожарного запаса воды;
- включение оповещения (светового/звукового) о пожаре в защищаемом объекте;
- визуализация всего технологического процесса на экранах АРМ оператора и панели оператора пожарного поста;
- хранение и отображение оперативных и исторических журналов на АРМ оператора и панели оператора за указанный период.
Комплексная система автоматического пожаротушения построена по распределенному принципу на базе программируемого логического контроллера. Каждый контроллер системы отвечает за функционирование законченного технологического участка, благодаря чему достигается повышенная отказоустойчивость системы.
Обычно при разработке систем автоматизации пожаротушения стремятся добиться следующих особенностей системы:
- гибкость;
- функциональность;
- совместимость.
Под гибкостью системы автоматизации пожаротушения понимают возможность доукомплектования системы соответствующими модулями, щитами, позволяющими решать те или иные задачи по автоматизации управления установками пожаротушения. Доукомплектование системы автоматизации пожаротушения может потребоваться при изменении количества защищаемых зон, при изменении алгоритма пожаротушения. Также гибкость системы автоматизации должна позволять выполнять изменение алгоритмов функционирования без изменения аппаратной комплектации. Для этого применяется перепрограммирование контроллеров системы.
Под функциональностью системы автоматизации пожаротушения понимают возможность реализации дополнительных режимов функционирования оборудования (имитация, тестирование, маскирование), защиты системы от несанкционированного доступа, осуществление контроля действия персонала по журналу событий.
Совместимость системы автоматизации пожаротушения предполагает применение тех же аппаратно-технических средств, что и для автоматизации технологических процессов на предприятии. Это позволяет сократить номенклатуру запасных частей и комплектующих, уменьшить затраты на освоение и обслуживание системы.
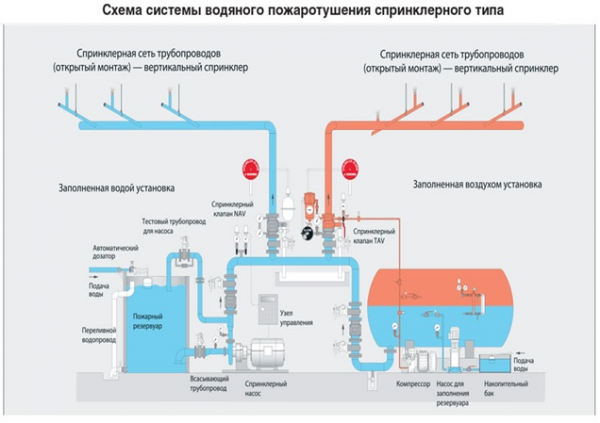
Глава 3. Структура системы автоматизации пожаротушения
Автоматическая система пожарной сигнализации и пожаротушения сушильного цеха АО «Апатит» организована по трехуровневому иерархическому принципу [1 – 3, 5]:
- нижний уровень;
- средний уровень;
- верхний уровень.
К нижнему уровню системы относятся:
- пожарные извещатели;
- звуковые и световые пожарные оповещатели;
- контрольно-измерительные приборы;
- устройства управления;
- исполнительные механизмы, а также устройства дистанционного запуска.
Устройства нижнего уровня должны располагаться непосредственно на контрольных точках объекта и на органах управления. Конструкция и исполнение устройств нижнего уровня позволяет им устойчиво и безопасно функционировать при самых неблагоприятных внешних условиях, а также во взрывоопасных и пожароопасных условиях. Связь устройств нижнего уровня с устройствами среднего уровня осуществляется с помощью соответствующих кабелей.
К среднему уровню системы относятся:
- шкафы процессорные;
- шкафы УСО (устройство связи с объектом).
Устройства среднего уровня должны быть расположены на территории цеха таким образом, чтобы минимизировать затраты на прокладку кабелей и снизить влияние помех.
К верхнему уровню системы относятся:
- АРМ;
- принтеры.
На рис. 3.1 приведена обобщенная схема многоуровневой автоматизации системы пожаротушения на АНОФ-2.
На рис. 3.2 показана схема системы автоматизации пожаротушения сушильного цеха с указанием участков обслуживания.
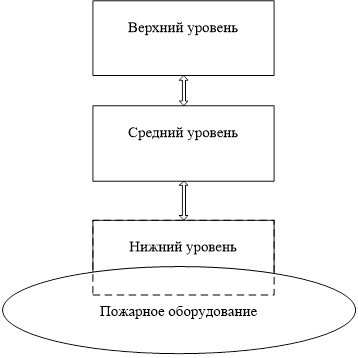
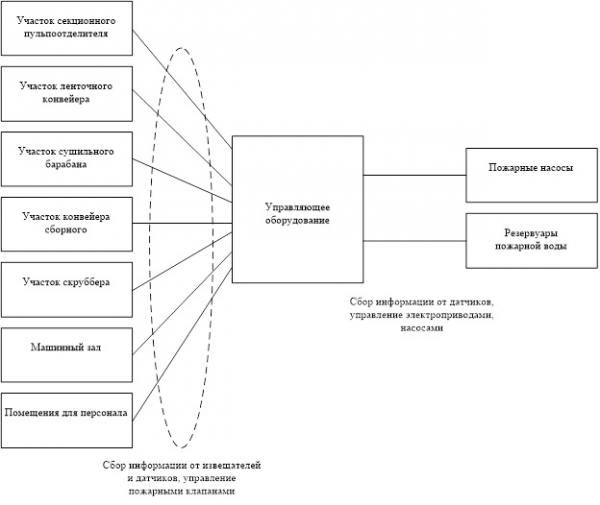
Детализированная структурная схема системы автоматизации пожаротушения сушильного цеха приведена на рис. 3.3. В состав системы автоматизации пожаротушения на среднем уровне входят модули ПЛК компании Эмикон. На основе этих модулей в промышленных условиях часто реализуются аналогичные системы. Кроме того, наличие в структуре системы автоматизации пожаротушения модуле й ПЛК обосновано тем, что на данных модулях выполнена автоматизация технологических процессов, связанных с выпуском основной продукции цеха. Использование однотипных модулей позволит сократить время на обслуживание систем автоматизации, упростит работу персонала службы автоматизации и оптимизирует формирование склада запасных частей для системы автоматизации. Кроме того, применение ПЛК в системе автоматизации пожаротушения необходимо для управления резервуаром пожарной воды и пожарными насосами.
Рассмотрим подробней структурную схему системы автоматизации (рис. 3.3).
На нижнем уровне автоматизации – датчики и исполнительные механизмы, установленные на пожароопасных участках, на резервуарах пожарной воды, на насосах пожарной воды подключаются к расположенным на среднем уровне модулям ввода или вывода ПЛК. В системе на среднем уровне применены следующие модули и устройства:
- CPU-31A – модуль центрального процессора ПЛК;
- AI-31A – модуль аналогового ввода;
- DI-32A – модуль дискретного ввода;
- CI-31A – модуль сбора сигналов от устройств RS485;
- CI-32A – модуль сбора сигналов от устройств HART;
- AO-31A – модуль вывода аналоговых сигналов;
- DO-31A – модуль вывода дискретных сигналов;
- ОПС БОЛИД – модуль охранно-пожарной сигнализации (ОПС) БОЛИД.
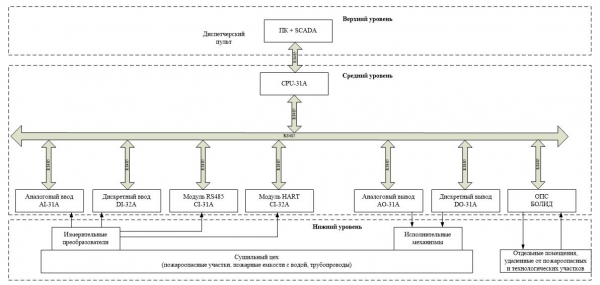
Охранно-пожарная сигнализация БОЛИД может полноценно выполнять все функции пожарной сигнализации, начиная от сбора информации от извещателей и заканчивая управлением звуковых и световых оповещателей. Применение ОПС БОЛИД в данном случае необходимо в помещениях цеха, удаленных от основных технологических участков, где задействованы ПЛК.
Шкаф с оборудованием среднего уровня системы автоматизации устанавливается в помещении насосной станции пожаротушения на стене.
На верхнем уровне системы автоматизации пожаротушения находится персональный компьютер (ПК) с установленным программным обеспечением системы сбора данных и диспетчерского управления (SCADA).
Программное обеспечение SCADA может взаимодействовать не только с оборудованием системы автоматизации пожаротушения, но и с оборудованием автоматизации технологических процессов сушильного цеха. Диспетчерский пульт устанавливается в помещении операторов с постоянным пребыванием дежурного персонала. При необходимости и при напряженной работе операторов АСУ основного технологического процесса, для системы автоматизации пожаротушения на верхнем уровне устанавливается отдельный компьютер с соответствующим программным обеспечением.
Диспетчерский пульт, устанавливаемый в помещении операторов, предназначен для отображения и индикации состояния оборудования, подключенного к ПЛК, модулям расширения, ОПС БОЛИД, а также для дистанционного пуска и останова установки пожаротушения.
Диспетчерский пульт обеспечивает:
- дистанционный пуск установки пожаротушения с пуском пожарных насосов;
- дистанционный сброс режима пожаротушения;
- автоматический контроль исправности связи с блоками управления;
- световую и звуковую сигнализацию о возникновении пожара (сигнал «Пожар») и о возникновении сигнала «Внимание».
Глава 4. Функциональная схема автоматизации системы пожаротушения
Система пожаротушения является водяной сплинкерной, с возможностью тушения водой из водопровода или пожарного резервуара. Движение воды по системе обеспечивает насосная станция. Насосная станция состоит из двух основных насосов (насос №1 и насос №2), «жокей-насоса» и резервного пожарного насоса. Система сплинкерного пожаротушения сушильного цеха состоит из четырех секций.
Рассмотрим функциональную схему автоматизации системы пожаротушения (рис. 4.1).
На данной схеме обозначены следующие позиции:
- SP 1-1 – манометр электроконтактный на выходе насоса № 1;
- SP 2-1 – манометр электроконтактный на выходе насоса № 2;
- SP 3-1 – манометр электроконтактный № 1 на выходе жокей-насоса;
- SP 4-1 – манометр электроконтактный № 2 на выходе «жокей-насоса»;
- SD 5-1 – датчик открытия клапана на входе системы пожаротушения;
- SP 6-1 – манометр электроконтактный № 1 на выходе пожарной насосной станции;
- SP 7-1 – манометр электроконтактный № 2 на выходе пожарной насосной станции;
- SDP 8-1 – сигнализатор давления жидкости на входе секции 1;
- SDP 9-1 – сигнализатор давления жидкости на входе секции 2;
- SDP 10-1 – сигнализатор давления жидкости на входе секции 3;
- SDP 11-1 – сигнализатор давления жидкости на входе секции 4;
- SDW 12-1 – сигнализатор потока жидкости на входе секции 1;
- SDW 13-1 – сигнализатор потока жидкости на входе секции 2;
- SDW 14-1 – сигнализатор потока жидкости на входе секции 3;
- SDW 15-1 – сигнализатор потока жидкости на входе секции 4;
- СПЖ – сигнализатор потока жидкости;
- СДУ – сигнализаторы давления жидкости.
Контроль давления в трубопроводах установки осуществляется манометрами электроконтактными (SP 1-1, SP 2-1, SP 3-1, SP 4-1).
Импульс на включение сигнализации о пожаре, о начале работы установки и прохождении огнетушащего вещества осуществляется от сигнализаторов давления (SDP 8-1, SDP 9-1, SDP 10-1, SDP 11-1).
Сигнализация о прохождении огнетушащего вещества по отметкам секций осуществляется от сигнализаторов потока жидкости (SDW 12-1, SDW 13-1, SDW 14-1, SDW 15-1).
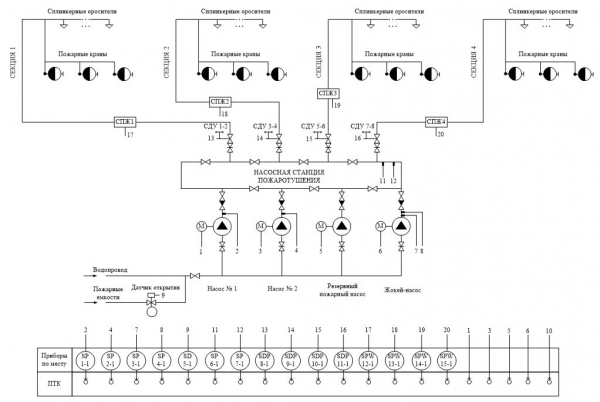
Поддержание давления в системе пожаротушения производится при помощи «жокей-насоса», управление которым производится от сигналов датчиков давления SP 6-1, SP 7-1. При падении давления в системе ниже установленных параметров датчика SP 7-1 срабатывают датчики SP 3-1 и SP 4-1, при срабатывании любого из них происходит пуск одного из основных пожарных насосов (насос № 1 или насос № 2).
В случае отказа пуска или невыхода одного из основных пожарных насосов (сигнал датчиков SP 1-1, SP 2-1) на режим в течение установленного времени (10 с), автоматически запускается резервный пожарный насос.
Разрушение теплового замка любого спринклера приводит к срабатыванию двух сигнализаторов давления жидкости. Сигналы с сигнализаторов давления жидкости и сигнализаторов потока жидкости поступают на оборудование среднего уровня автоматизации. Средний уровень автоматизации выдает импульс на отключение систем вентиляции участков, где возникло возгорание, и управляет технологическим оборудованием для пожаротушения.
Для управления процессом наполнения пожарного резервуара также используется система автоматического автоматизации. На рис. 4.2 показана функциональная схема автоматизации пожарного резервуара. На данной функциональной схеме обозначены позиции:
- SD 1-1 – датчик открытия клапана на входе наполняющего насоса;
- SP 2-1 – датчик давления на выходе наполняющего насоса;
- SHA 3-1 – датчик уровня воды в пожарном резервуаре;
- SHI 4-1 – датчик верхнего аварийного уровня;
- SHI 5-1 – датчик нижнего аварийного уровня.
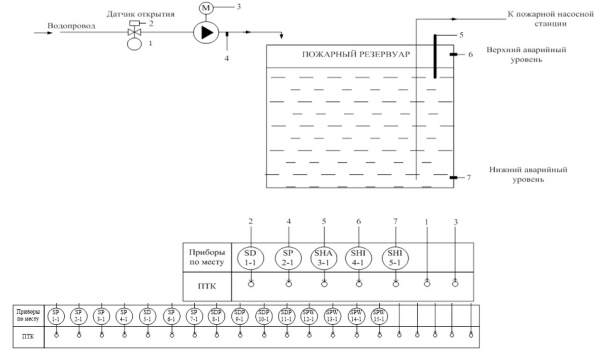
1