Трубопроводный транспорт – один из наиболее эффективных и экономичных средств транспортировки газообразных веществ. Это – экологически чистый вид транспорта, обладает низкой себестоимостью, непрерывностью процесса перекачки, возможностью повсеместной укладки и т.д. Использование трубопроводного транспорта более эффективно, чем использование автомобильного и железнодорожного транспорта, позволяет уменьшить степень риска при транспортировке газовых сред.
Функционирование трубопроводов происходит в жестких условиях, поскольку они подвергаются различным нагрузкам – внутреннему давлению, осевым растягивающим или сжимающим напряжениям, давлению грунта засыпки и подвижных средств, перепадам температур.
Все эти факторы способствуют развитию коррозии на внутренней и внешней поверхности стенки трубопровода, и, как следствие – возникновению утечек и аварий. Именно по этой причине большее внимание уделяется надежности и эффективности работы магистральных трубопроводов.
Актуальность темы
С каждым годом экологическое состояние нашей окружающей среды все ухудшается и ухудшается… Постоянно увеличивается количество факторов, негативно влияющих на окружающую природную среду – растет количество промышленных предприятий, а вместе с ними увеличивается и количество вредных выбросов. Именно поэтому «ужесточаются» требования к качеству оборудования, к его надежности (для обеспечения необходимой экологической безопасности).
Не обходят стороной эти требования и газовую промышленность. Снижение негативного воздействия и влияния магистральных трубопроводов на окружающую среду в процессе их возведения и эксплуатации является одной из приоритетных задач современного строительства, поэтому разработка технических решений в целях повышения надежности трубопроводов и снижения антропогенного воздействия на окружающую среду является актуальной проблемой на сегодняшний день.
Цель и задачи исследования
Основной целью работы является разработка методов повышения эксплуатационной надежности трубопроводных систем, транспортирующих газовые среды.
Основные задачи исследования:
Повышение эксплуатационной надежности трубопроводных систем, транспортирующих газовые среды
Магистральные трубопроводы являются составной частью мировой системы транспортировки газообразных продуктов. Рассмотрим более подробно эти системы [ 1 – 2 ].
С месторождений газ поступает через газосборный пункт по промысловому коллектору на установку подготовки газа, где производится осушка газа, очистка от механических примесей, углекислого газа и сероводорода. Далее газ поступает на головную компрессорную станцию, а затем – в магистральный газопровод (рис. 1).
Способы повышения надежности трубопроводов
... и с применением специальных комплексов . Повышение надежности эксплуатации магистральных трубопроводов, связанное с увеличением точности оценки коррозионной ... восстановительные работы здесь требуют значительных материальных и финансовых затрат, и в части охраны окружающей среды. ... и ремонтных работ без какого-либо влияния на транспорт углеводородов. На повышение надежности трубопроводной системы ...
Рисунок 1 – Типовая схема расположения оборудования магистрального газопровода
1 – промыслы; 2 – газосборный пункт; 3 – промысловый коллектор; 4 – установка подготовки газа; 5 – головная компрессорная станция (КС); 6 – магистральный трубопровод; 7 – промежуточная КС; 8 – линейные запорные устройства; 9 – подводный переход с резервной ниткой; 10 – переход под железной дорогой; 11 – отвод от магистрального газопровода; 12 – газораспределительная станция (ГРС); 13 – конечная ГРС; 14 – станция подземного хранения газа (СПХГ); 15 – газорегуляторный пункт (ГРП); 16 – тепловая электростанция; 17 – газоперерабатывающий завод (ГПЗ).
Для эффективной работы трубопровода необходимо поддержание давления газа по всей длине трассы – для этого устанавливаются компрессорные станции (КС) с интервалом 80 – 120 км.
Объекты КС проектируют в блочно–комплектном исполнении. В большинстве случаев КС оборудуются центробежными нагнетателями с приводом от газотурбинных установок или электродвигателей. В настоящее время газотурбинным приводом оснащено более 80% всех КС, а электроприводом – около 20%.
К линейным сооружениям относят собственно магистральный трубопровод, линейные запорные устройства, узлы очистки газопровода, переходы через искусственные и естественные препятствия, станции противокоррозионной защиты, дренажные устройства, а также линии технологической связи, отводы от магистрального газопровода для подачи части транспортируемого газа потребителям и сооружения линейной эксплуатационной службы (ЛЭС) [ 3 – 4 ].
Расстояние между линейными запорными устройствами (кранами) должно быть не более 30 км. Управление линейными кранами следует предусматривать дистанционным из помещения операторной компрессорной станции, а также ручным по месту. Линейная запорная арматура должна оснащаться автоматическими механизмами аварийного перекрытия.
При параллельной прокладке двух и более магистральных газопроводов в одном технологическом коридоре предусматривается соединение их перемычками с запорной арматурой. Перемычки следует размещать на расстоянии не менее 40 км и не более 60 км друг от друга у линейных кранов, а также до и после компрессорных станций.
Газораспределительные станции (ГРС) предназначены для снижения (редуцирования) давления газа до рабочего давления газораспределительной системы потребителей. ГРС также оборудуются узлами учета и установками очистки и одоризации газа (придания ему специфического запаха для облегчения обнаружения утечки газа с целью предупреждения взрывоопасных ситуаций и отравления людей).
Обработка металлов давлением (3)
... относительное удлинение которых при разрыве может достигать сотен процентов. Обработка металлов давлением может осуществляться над сплавами, обладающих высокой пластичностью такими как: низкоуглеродистые ... ниже, что позволяет применять более простое оборудование и инструмент. Обработка металлов давлением может происходить несколькими методами, например: прокатка, прессование, волочение, ковка , ...
После ГРС газ поступает в газовые сети населенных пунктов, которые подают газ к месту потребления. Снижение и поддержание в необходимых пределах давления газа в газораспределительных сетях осуществляется на газорегуляторных пунктах (ГРП).
К крупным потребителям газа также относятся тепловые электростанции и газоперерабатывающие заводы (ГПЗ).
Для сглаживания неравномерности потребления газа крупными населенными пунктами сооружаются станции подземного хранения газа (СПХГ).
Для закачки газа в подземное газохранилище СПХГ оборудуется собственной компрессорной станцией.
К вспомогательным линейным сооружениям магистрального газопровода относят линии связи, вдольтрассовые дороги, вертолетные площадки, площадки аварийного запаса труб, усадьбы линейных ремонтеров и т.д.
В зависимости от конкретных условий эксплуатации состав сооружений магистрального газопровода может изменяться – на газопроводах небольшой протяженности может не быть промежуточных КС. Если в добываемом газе отсутствует сероводород или углекислый газ, то необходимость в установках по очистке газа от них отпадает. Станции подземного хранения газа сооружаются не всегда.
Исходя из величины рабочего давления, магистральные газопроводы подразделяются на два класса [ 5 ]:
1–й класс – при рабочем давлении свыше 2,5 МПа до 10 МПа включительно;
2–й класс – при рабочем давлении свыше 1,2 МПа до 2,5 МПа включительно.
Протяженность магистральных газопроводов составляет обычно от нескольких десятков до нескольких тысяч километров, а диаметр – от 150 до 1420 мм включительно. Большая часть газопроводов имеет диаметр от 720 до 1420 мм включительно.
В процессе эксплуатации трубопроводы подвергаются различным нагрузкам – внутреннему давлению, давлению грунта засыпки и подвижных средств, перепадам температур, осевым растягивающим или сжимающим напряжениям. Эти факторы способствуют развитию коррозии на стенках трубопровода – а это, как известно, является основной причиной возникновения аварий.
Защита трубопроводов от коррозии
Трубопровод, уложенный в грунт, подвергается почвенной коррозии, а проходящий над землей – атмосферной. Коррозией металлов называется разрушение или изменение его свойств, вызванное химическими или электрохимическими процессами при взаимодействии с окружающей средой. По характеру взаимодействия металла с окружающей средой различают два основных вида коррозии: химическую и электрохимическую [ 6 – 7 ].
Химическая коррозия относится к случаям изменения свойств металла в результате химических реакций без возникновения и протекания электрического тока. К этому виду коррозии относятся газовая коррозия и коррозия в неэлектролитах.
Газовая коррозия происходит в результате взаимодействия металла с сильно разогретым газом при полном отсутствии влаги (например, коррозия лопаток газовых турбин, образование окалины при термической обработке металла и т.п.).
Коррозия в неэлектролитах – разрушение металла в жидких или газообразных неэлектропроводных средах (коррозия при взаимодействии с нефтепродуктами, содержащими серу).
Электрохимическая коррозия – это окисление металлов в электропроводных средах, сопровождающееся образованием и протеканием электрического тока. При этом на различных участках поверхности металла возникают анодные и катодные участки. Коррозионные разрушения образуются только на анодных участках.
Защита нефтепромысловых трубопроводов от коррозии
... способы защиты трубопроводов от коррозии. 1. Виды коррозии Коррозия в зависимости от механизма реакций, протекающих на поверхности металла, подразделяется на химическую и электрохимическую. Химическая коррозия представляет собой процесс разрушения металла при взаимодействии с сухими газами (газовая коррозия) или ...
К электрохимическим коррозионным процессам относятся:
- коррозия в электролитах (жидкостях, проводящих электрический ток: речная и морская вода, растворы солей, кислот и щелочей);
- почвенная коррозия – разрушение металла под воздействием почвенного электролита;
- контактная коррозия – коррозия металлов в присутствии воды, вызванная непосредственным контактом двух и более металлов, имеющих разный электрохимический потенциал;
- атмосферная коррозия – разрушение металла в среде атмосферного воздуха или любого другого влажного газа;
- биокоррозия – коррозия, жизнедеятельностью микроорганизмов, которые выделяют вещества, ускоряющие коррозионные процессы.
Процесс коррозии металла начинается с его поверхности и распространяется вглубь (рис. 2).
Различают сплошную и местную коррозию.
При сплошной коррозии вся поверхность металла покрыта слоем продуктов коррозии. Неравномерность сплошной коррозии прямо пропорционально зависит от агрессивности коррозионной среды.
Местная коррозия – разрушение металла на отдельных участках поверхности. Различают следующие виды местной коррозии:
- пятнами (толщина слоя продуктов коррозии много меньше площади пятна);
- язвенная (глубина повреждения значительна и соизмерима с его площадью);
- точечная (питтинговая) – глубина повреждения много больше его диаметра. Точечная коррозия может перейти в сквозную при благоприятных условиях коррозионных процессов;
- подповерхностная – вспучивание в виде пузырей и расслоение металла;
- межкристаллитная (распространяется по границам кристаллов металла и приводит к потере прочности и пластичности);
- структурно–избирательная (разрушается какой–либо один элемент сплава);
- коррозионное растрескивание (происходит в результате сочетания коррозионного и механического воздействия на металл).
Рисунок 2 – Основные виды коррозионных разрушений
Местная коррозия является причиной возникновения концетраторов напряжений, поэтому она более опасна, чем сплошная.
На интенсивность протекания процессов коррозии оказывают влияние различные факторы (рис. 3 и 4):
- неоднородный состав стали (содержащиеся в стали легирующие добавки и примеси благоприятствуют образованию коррозионных пар в агрессивной среде);
- неоднородность условий на поверхности металла (наличие царапин, вмятин, сварных швов, окалины на поверхности металла приводит к образованию анодных и катодных участков и является очагами коррозии);
- неоднородность условий окружающей среды: различная влажность грунта в области прокладки трубопровода и различная аэрация (доступ кислорода к участкам трубопровода);
- неоднородность транспортируемой среды (наличие воды и растворенных солей может привести к образование ручейковой коррозии на внутренней поверхности трубопровода).
- повысить электропроводность;
- увеличить теплопроводность, теплостойкость, температуру воспламенения;
- придать антистатические свойства;
- улучшить механические характеристики (прочность при растяжении и на разрыв;
- увеличить модуль упругости и предельное растяжение;
- повысить износостойкость);
- увеличить адгезионную прочность и расширить температурный диапазон применения (от – 60 до 250°С);
- обеспечить устойчивость к воздействию агрессивных рабочих сред.
- Нечваль Андрей Михайлович. Проектирование и эксплуатация газонефтепроводов: Учеб. пособие / Уфимский гос. нефтяной технический ун–т. – Уфа: ООО ДизайнПолиграфСервис, 2001. – 166 с.
- Селезнев В.Е., Прялов С.Н. Методы построения моделей течений в магистральных трубопроводах и каналах / М.: Едиториал УРСС, 2012. – 560 с.
- Техника и технология транспорта и хранения нефти и газа / Ф.Ф. Абузова, Р.А. Алиев, В.Ф. Новоселов и др. – М.: Недра, 1992. – 320 с.
- Трубопроводный транспорт нефти и газа / Р.А. Алиев, В.Д. Белоусов, А.Г. Немудров и др. – М.: Недра, 1988. – 368 с.
- СНиП 2.05.06–85*. Магистральные трубопроводы / Госстрой России.: ГП ЦПП, 1997. – 52 с.
- Ясин Э.М., Черникин В.И. Устойчивость подземных трубопроводов / М.: Недра, 1967 г., 120 с.
- Противокоррозионная защита трубопроводов и резервуаров / М. В. Кузнецов, В. Ф. Новоселов, П. И. Тугунов и др. – М.: Недра, 1992. – 238 с.
- Научно–технический журнал «Наноиндустрия», от 07 мая 2009 г.
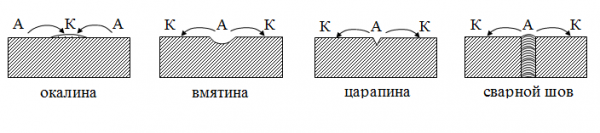
Методы защиты от коррозии металлов и сплавов
... метод осаждения защитных металлических покрытий получил очень широкое распространение в промышленности. По сравнению с другими способами нанесения металлопокрытий он имеет ряд серьезных преимуществ: высокую экономичность (защита металла от коррозии ... распределенным по всей поверхности, непроницаемым для окружающей среды, иметь высокую адгезию (прочность сцепления) к металлу, быть твердым и ...
Рисунок 3 – Влияние микроструктуры поверхности металла на интенсивность процесса коррозии
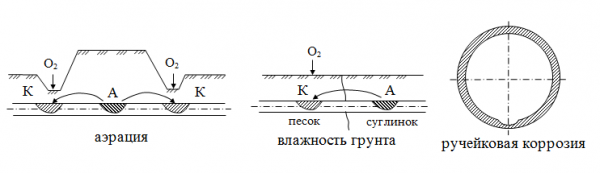
Рисунок 4 – Влияние неоднородности среды на интенсивность процесса коррозии
Основные способы защиты трубопроводов от коррозии
Способы, продляющие срок службы трубопровода, условно разделяют на четыре группы.
– Пассивная защита. Заключается в нанесении на поверхность трубы защитного изоляционного покрытия на основе битума, полимерных лент или напыленного полимера. Изоляционные покрытия должны обладать сплошностью, высокой диэлектрической способностью, адгезией, механической прочностью, водонепроницаемостью, эластичностью, биостойкостью, термостойкостью, долговечностью и недифицитностью.
– Введение в металл компонентов, повышающих коррозионную стойкость. Метод применяется на стадии изготовления металла. Одновременно из металла удаляются примеси, понижающие коррозионную устойчивость.
– Воздействие на окружающую среду. Метод основан на введение ингибиторов коррозии для дезактивации агрессивной среды.
– Активная защита. К этому методу относятся катодная, протекторная и дренажная защита.
Чаще всего применяется метод пассивной защиты – покрытие внутренней и внешней стенок трубы изоляционными материалами. В последние годы для повышения прочностных свойств и износостойкости изоляционных материалов и покрытий применяют их армирование наноструктурными наполнителями [ 8 ].
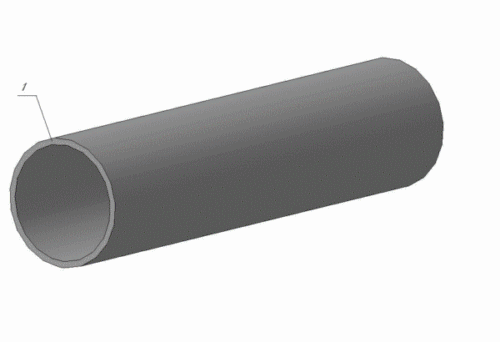
Рисунок 5 – Слои изоляции
(анимация: 5 кадров, 5 циклов повторения, 72 килобайта)
1 – труба; 2 – слой хромата; 3 – слой адгезива; 4 – слой эструдированного полиэтилена с наноструктурными наполнителями; 5 – слой внутренней изоляции
Созданные с использованием нанотехнологий материалы поднимут на новый уровень качество труб с антикоррозионным покрытием. Это повысит их конкурентоспособность, увеличит срок эксплуатации и изменит физико–химические свойства покрытий. Это обстоятельство немаловажно в связи со строительством газопроводов в сложных климатических условиях территорий с большими и резкими колебаниями температур.
Применение углеродных нанотрубок и углеродных нановолокон как наполнителей полимеров позволяет улучшить ряд показателей:
Выводы
Таким образом, можно сделать вывод, что определяющим критерием экологической безопасности трубопроводных систем является их конструктивная надежность – один из основных показателей качества любой конструкции (системы), заключающаяся в ее способности выполнять заданные функции, сохраняя свои эксплуатационные свойства в течение требуемого промежутка времени «жизненного цикла».
Монтаж и эксплуатация газопроводов микрорайона и защита их от коррозии
... Также установлена 1 катодная станция защиты газопровода от коррозии. В микрорайоне имеются подземные коммуникации: газопровод, водопровод, теплопровод. 1.2 Устройство и прокладка газопроводов Прокладка газопровода, это сложный и трудоемкий ... быть запорным, если оно служит для герметичного отделения одной части газопровода от второй, и дроссельным, если его основная задача заключается в точном ...
Отказ магистрального газопровода, проявляющийся в местной потере герметичности стенки трубы, трубных деталей или в общей потере прочности в результате разрушения, приводит, как правило, к значительному экологическому ущербу с возможными непоправимыми последствиями для окружающей природной среды.
Одним из способов предотвращения разрушения стенки трубопровода является использование новых высококачественных материалов для изготовления изоляционных покрытий.
Добавление при изготовлении изоляционных покрытий углеродных нановолокон – эффективный способ улучшения физико–механических характеристик изоляционных материалов на основе полиэтилена – прочность и износостойкость полимерного материала на основе сверхмолекулярного полиэтилена повышается в несколько раз, коэффициент трения снижается.
При написании данного реферата магистерская работа еще не завершена. Окончательное завершение: декабрь 2013 года. Полный текст работы и материалы по теме могут быть получены у автора или его руководителя после указанной даты.
Список источников
[Электронный ресурс]//URL: https://drprom.ru/referat/nadejnost-gazonefteprovodov/